OUR SERVICES
As a true expert in the construction of specialist machinery, with a strong parent company behind us, we can guarantee continuity and continuous development.
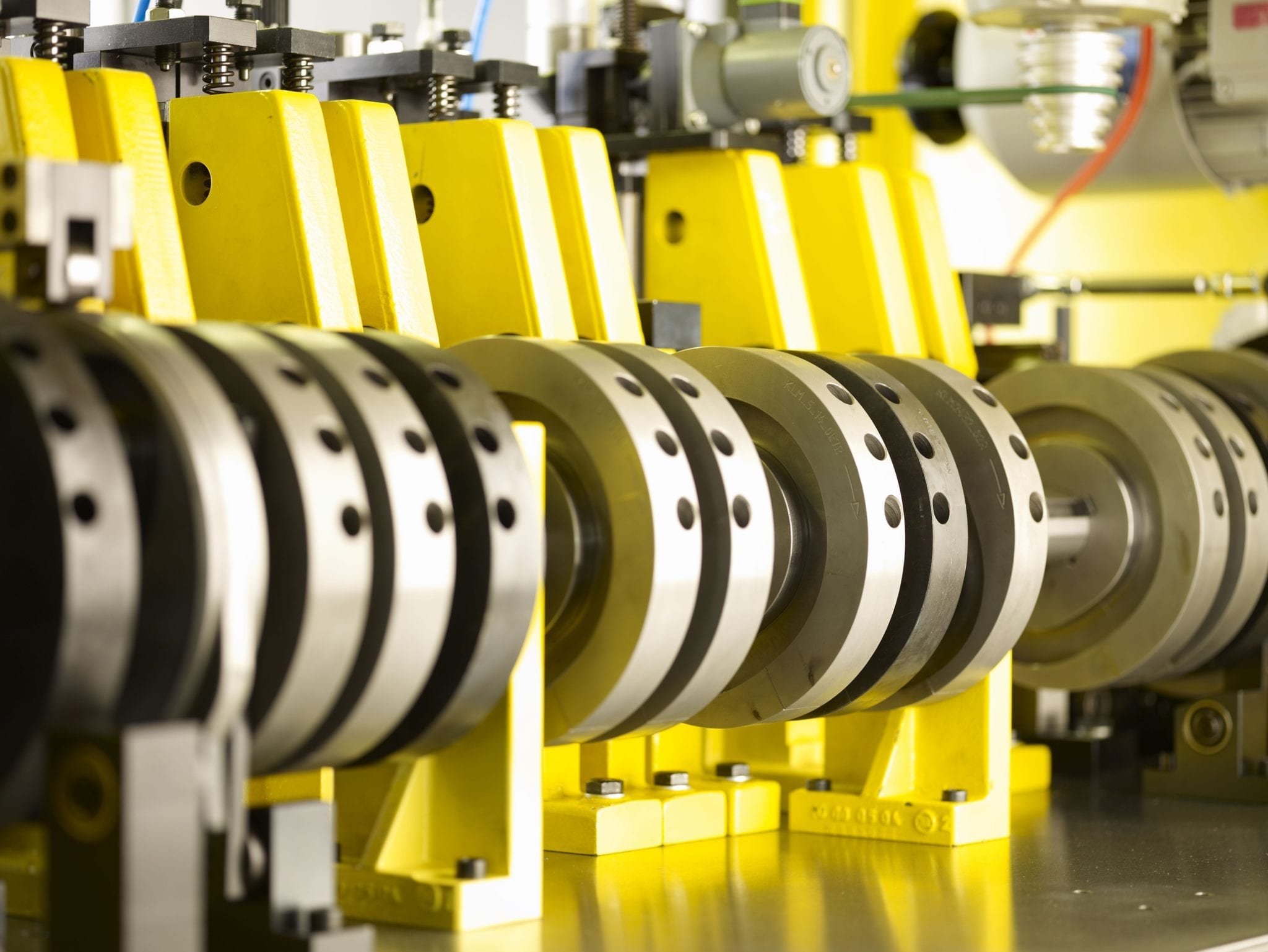
The concept of the in-line machine was clear from the outset. Therefore, the different units have been and continue to be designed in such a way that they can also be retrofitted to the old machines.
We provide ongoing support and service for our machines – through improvements, modifications, maintenance, instruction or conversion to new products.
Our machines come with over 30 years of experience. And this experience is incorporated into the design, the mechanics, the electrics and the tools.
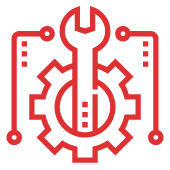
Mechanical Engineering
Our machines are based on stable, welded steel structures. The machine table is polished for the setup of the machining station. Chains are used to shift the transport plates with the parts by 2" or 4" from one station to another. Each part is positioned separately for each stage of the machining. The tool advance is normally controlled by means of curves, but it can be controlled via a servo motor or NC controller if necessary. The tool spindles are powered by three-phase current motors, with servo motors, frequency-controlled motors or high-frequency motors where required. The control cabinet is screwed to the machine on the front side, and all electrical components of the machine are hard-wired. A movable oil tank with a chip conveyor is pushed under the machine, and from there the oil is pumped into the machine via a filter. The oil mist is extracted via an electrostatic suction system on the machine roof. The machine is sealed on all sides; at the front and back by three sealed windows on each side.
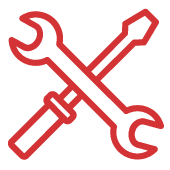
Tool Construction
Essentially, the machines are equipped with our tools. However, if customers have existing tools, they can provide them and we can adjust our adaptors or tool holders to their tools.
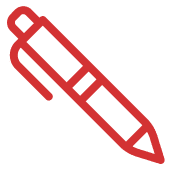
Training
Once a machine is completed, it is prepared for a trial run in our factory. We recommend customers to send their responsible personnel to check the performance and quality of the machine and, at the same time, be trained in the workings of the machine. This can take one or two weeks for new customers. For existing customers, it normally takes around one or two days.
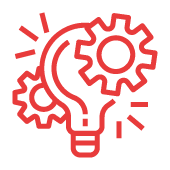
Conversions
We build for eternity, but mostly the parts produced on the machine are discontinued before there are any issues with the condition of the machine. So it is quite common that machines need to be converted for a follow-up component or a completely new part. Experienced customers can make minor conversions with our support or request one of our fitters. However, for major conversion jobs, we recommend moving the machine to our workshop. .
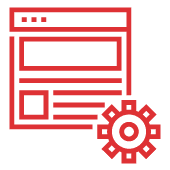
Maintenance
The machines are designed to be virtually maintenance-free. The arrangement of the oil lines cools the tools, lubricates the moving parts and rinses away the chips. A plan is also provided with the machine for further maintenance.
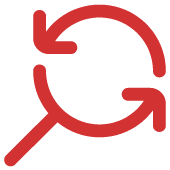
Spare Parts
Even at the design phase, we make sure that we use standard components. For customers, this means they only require a small stock of spare parts even if they have a large number of different machines. At the same time, it also means that we at Linematic always have the standard spare parts available. .